To protect it, i place it in the mold behind one thin layer of tight weave glass (which also helps to produce the glass like surface) and then support it with an even thicker layer of glass, followed by a thin layer of glass. The basics of carbon fiber epoxy infusion.
Diy Vacuum Pump For Bagging Rc Plane Wings - Youtube
Vacuum bags are used to hold the layers together, removing air and impregnating the fibers with the epoxy.
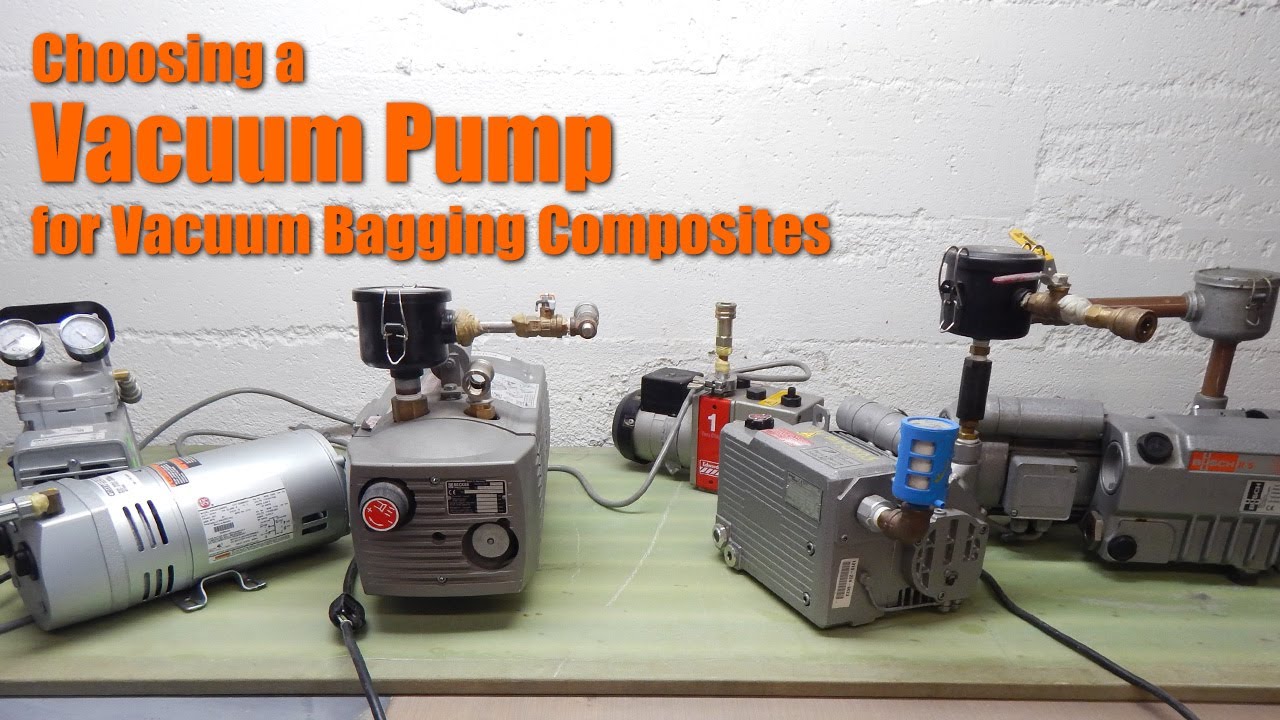
Diy vacuum pump carbon fiber. Once the vacuum begins, all of the air is removed from the fiber, forcing the resin into the voids, ensuring the strength aspect. Molding, wrapping and news are all available here to the diy carbon fiber crowd. Learn how to make carbon fiber parts.
1.) a mold to place your carbon fiber on that is wetted out with resin to cure on in the shape of the part you want. Just a vacuum pump, some inexpensive materials to build a vacuum bag and a lot of determination. Our release fabric will make sure there isn't too much in the final layup.
These kits include all of the materials you need to give vacuum infusion a try on your own. 2.) an air tight enough bag to hold the negative pressure of the vacuum and thus the part to the mold. This is the same process used in race cars, aircraft, and yacht building.
The carbon fiber is brittle though (due in part to it's chemical make up and it's stiffness. Read our next post on trimming carbon fiber parts to learn how we do it! If you feel noticeably less resistance after pumping the bag down, you have a leak or significant outgassing.
The fiberglass supply 1.5 quart resin trap w/vacuum gauge should be good enough for just about anyone. Vacuum pump can be used for vacuum bagging, veneer, or if you are building anything with fibergla. Assuming the pump is working right, the resistance will top out at about 5/6 of a full throw.
The upper portion of the mold is made from a. Leave the vacuum running to insure the integrity of your tool surface and prepare your layup, in our case it will be a layer of bid fiberglass and two layers of bid carbon fiber with the fiberglass applied against the tool (the ultimate outside surface of the canopy frame). Pour more epoxy into the middle and work outwards.
This pump displaces 1.2 cfm and will achieve a maximum vacuum pressure of 24.0″ hg. The amount of resin is applied to the fiber prior to enclosing it for vacuum application. The part should remain under full vacuum until the resin has cured.
The resin on the mould should help to 'stick' the carbon cloth in place whilst you begin to press the carbon fibre cloth more thoroughly into the surface of the mould, driving the resin through the cloth as you do. It is a practical pump for small vacuum bagging projects. Ad get auto parts, spare parts, fluids & chemicals and accessories at great prices.
You can use these kits to produce parts entirely from carbon fiber, kevlar, fiberglass or any other composite material. Ad get auto parts, spare parts, fluids & chemicals and accessories at great prices. This is important to work out any air bubbles or wrinkles in the carbon fiber.
You don’t need an autoclave or a lot of fancy equipment. You can use these kits to produce parts entirely from carbon fiber, kevlar, fiberglass or any other composite material. Just stop up the end of the hose, and pull on the pump, and feel the resistance to calibrate your judgment of the vacuum level.
Carbon fiber has a resin to fiber ratio which provides the optimum strength. Pump types vacuum pump types include piston, rotary vane, turbine, diaphragm, and venturi. These kits include all of the materials you need to give vacuum bagging a try on your own.
3.) a large enough and thin enough bag to have the flexability to hold the carbon fiber tight to the mold while it cures This will prevent you from sucking epoxy. Perfect vacuum resin infusion of a carbon fiber.
Four layers with carbon fiber sandwiched in between. This guide even outlines the construction of a vacuum pump needed for that step. This is typically measured by weight.
The lower mold is rigid, and commonly made from fiberglass and coated with gelcoat. Now that you’ve successfully infused a beautiful carbon fiber part, it’s time to trim off the raw edges. Lay the carbon fiber down and position it.
Make A Manual Vacuum Pump For Under 20 By Converting A Bicycle Pump 8 Steps With Pictures - Instructables
Hand Laminate Vacuum Bag A Simple Carbon Fibre Part Inc Vacuum Cleaner Method - Youtube
Want To Vacuum Bag Your Carbon Fiber Or Fiberglass Composite Parts This Kit Will Get You Started Fiberglass Mold Carbon Fiber Vacuum Bags
Vacuum Bagging Kit 14 Hp Diy - Do It Yourself Kit For Carbonglass Composite Amazonin Industrial Scientific
Vacuum Pumps For Resin Infusion
Composites Tips
Vacuum Bagging Basics - Everything You Need To Get Started - Epoxyworks
Composites Tips
How To Choose A Vacuum Pump For Vacuum Bagging Composites - Youtube
Dvp Ec4 Composites Vacuum Pump For Vacuum Bagging - Product Demo - Youtube
Vacuum Infusion Equipment And Methods - Part One - Fibre Glast
Homemade Vacuum Pump For Vacuum Bagging Carbon Fiber And Fiberglass - Youtube
Vacuum Assisted Resin Infusion Process - Youtube
Vacuum Bagging Kit - Play With Carbon - Australia
Vacuum Bagging Equipment And Methods Fibre Glast
Vacuum Bagging Basics 16 Steps - Instructables
Vacuum Bagging Equipment And Methods Fibre Glast
Composites Tips
Composites Tips